Custom Synthesis
Tailor made manufacturing
We manufacture individual, innovative and sophisticated products, applying our kilo lab facilities to seamlessly transfer projects from research to pilot scale and exclusive synthesis at full production scale. This includes performing complex multi-step syntheses.
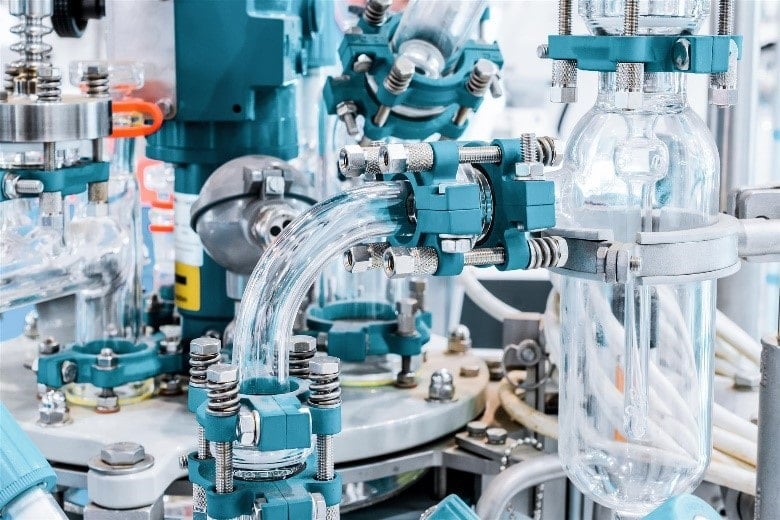
Kilo lab
Initial quantities of expensive intermediates can be delivered flexibly and in less time compared to a pilot plant, shortening the customer’s time-to-market.
Pilot & Scale-up
By providing reliable scale-up from lab development to pilot production, we help achieve ambitious project deadlines. Our team‘s taking care of punctual delivery, based on state-of-the-art chemical and technical expertise, frees up customers‘ resources to be applied elsewhere.
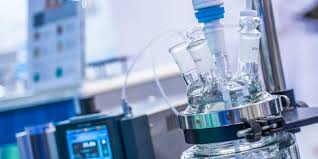
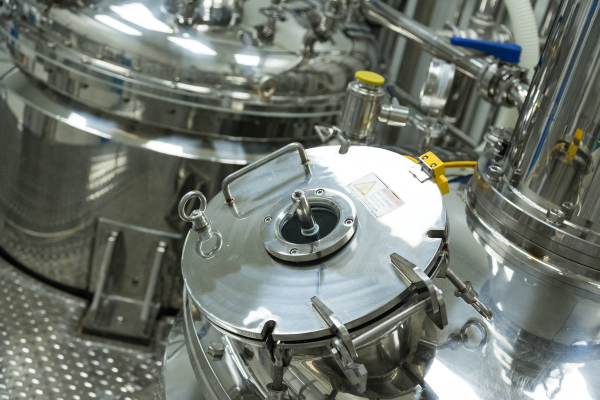
Exclusive synthesis
At two production plants in the industrial park Frankfurt-Höchst, we perform complex, individual multi-step syntheses in more than 80 reactors in various materials ranging from 100 and 5,000 liters, delivering quantities of up to several metric tons.
The flexible design of our assets enables a broad variety of chemical transformations and unit operations, while the close proximity of development, scale-up and commercial manufacturing plants saves time and cost in delivering a project.
Markets
A long track record in the manufacturing of organic electronic materials for:
Organic LED (OLED) for displays
Organic Photovoltaic (OPV)
Organic Photodetector (OPD)
Liquid crystal building blocks in high purity
Materials for batteries
Phosphorus-containing ligands and others (Large commercial and midsize scale)
Metallocenes and homogeneous catalysts
Pilot and midsize plants from 10 kg up to tons scale offering high flexibility
Advanced technologies: Low-temperature, e.g. for boronic acids and high pressure reactions for e.g. chiral compounds
Extended capacities for chemical process development at lab scale for contract research
Process development for applications of bio-based materials
Applied technologies are hydrogenation, oxidation or purifications via rectification or crystallization
- Piloting of new products
- Manufacturing of test and tox quantities in a range of 100 kg up to tons per campaign
- Large scale manufacturing at sites within the WeylChem network
Capabilities
Reactors from 10 to 100 liter constructed of glass, stainless steel and glass-lined steel and other materials as required
Distillation units
Thin film evaporators
Range of filtration units
Heating and cooling system
Vacuum drying cabinets
Option for direct connection to up and downstream units in the pilot plant at 300 to 500 liter
Examples of key technologies used in large scale:
Acylation
Alkylation
Amination
Bromination
Carbonylation
Carboxylation
Chlorination
Chlorosulfonation
Cross coupling
Diazotization
Diels-Alder reaction
Friedel-Crafts reactions
Grignard reaction
Hartwig-Buchwald coupling
Heck reaction
Hydroformylation
Hydrogenation
Lithium alanate reduction
Melt reactions at high temperatures
Nitration
Organometallic reactions, e. g. with BuLi or HexLi
Organophosphorus chemistry
Polymerization or polycondensation
Reductive amination
Sodium boro-hydride reduction
Sulfonation (also with oleum)
Suzuki coupling
Ullmann reaction
Capabilities
Advanced reactors with capacities of 100 l, 500 l and 1000 l can be operated via a heating/cooling circuit with an inert heat-transfer medium in the range from -100 °C to +200 °C.
Air-sensitive raw materials (e.g. Grignard-, butyl lithium-, lithium alanate-solutions, etc.) are metered from safety boxes. The reactors are DCS-controlled and equipped with on-site operator terminals. If required, they can quickly be linked to a number of conventional upstream and downstream reactors:
Products
Various specialty chemicals including
Complex aldehydes
Organic boronic acids
Coupled aromatic ring systems
Homogenous catalysts
Building blocks for API-synthesis and materials for organic electronic
Capabilities
Reactions including hydroformylations, carbonylations and hydrogenations performed in the presence of catalysts under high pressure to achieve the required conversion, selectivity and yield.
Special high-pressure autoclaves
26 lab autoclaves of 0.2 to 1 liter up to 750 bar, 300 °C in different materials for process development
Piloting: 7 autoclaves from 5 to 300 liter up to 200 bar, 300 °C
Hastelloy up to 1.6 m³ (up to 200 bar, 200 °C)
Stainless steel up to 1.8 m³ (up to 100 bar)
Compressors and gas-supply stations
Carbon monoxide
Ethylene and Hydrogen from pipeline
Pre-formation and handling of air-sensitive homogenous catalysts
Products
Enantiomeric alcohols (e.g. based on ketones)
Carboxylic acid esters and amides
- Flexible, variably connectable equipment for complex multi-stage synthesis
- Total stirred reactor capacity >50 m3
- 80 different reaction vessels from 0.1 up to 5.0 m3
- Stirred pressure filters up to 4 m2
- Thin film evaporators up to 1.0 m2
- Short path evaporators up to 0.3 m2
- Distillation columns up to 30 theoretical plates
- Materials: Stainless steel, glass-lined steel, Hastelloy, glass
Related Topics
Interested in our services or looking for more information?
Please fill out the form below in order to get in touch with the responsible person who will contact you as soon as possible.